PART I: Is MES Still Relevant In a World Embracing Artificial Intelligence?
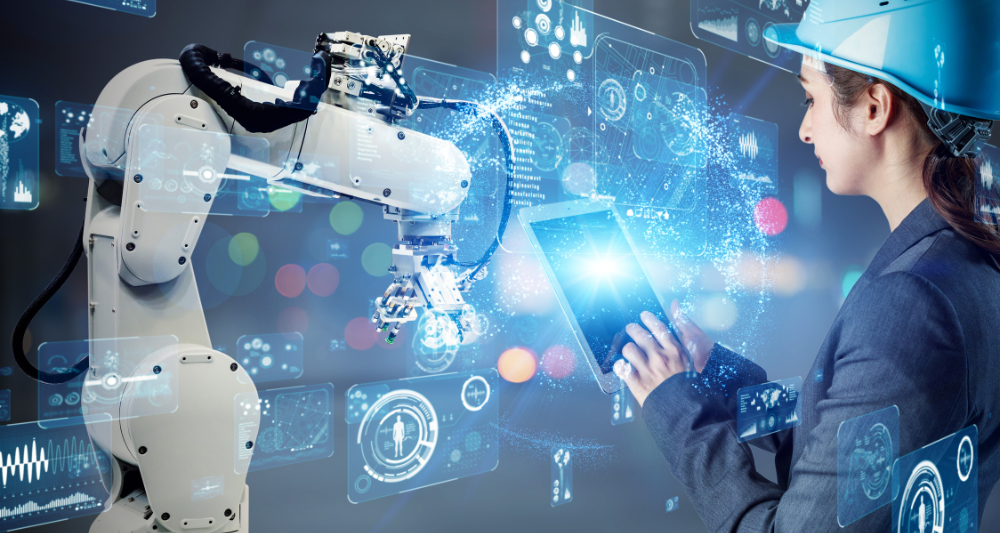
I was recently thinking about MES (manufacturing execution systems) and if they are still relevant in today’s world. Most companies are talking about artificial intelligence (AI) and machine learning (ML) since they have a desire to do more with their data. Vendors are highly focused on software that helps achieve these goals. Thus, the question is, should companies still look at their MES solution? Should they keep what they have now? What role does MES have in a rapidly advancing technological world? To answer those questions, let’s reflect on the evolution of MES and manufacturing in the last 20 years.
Let’s start with the basics; MES is a software program created to oversee and enhance production operations. MES plays a role in boosting efficiency, resolving production line issues swiftly and ensuring transparency by collecting and analyzing real time data. Essentially its software is designed to work inside of a manufacturing environment and be leveraged by operators, supervisors, and management to capture and review key production data with the goal of constant improvement. A well-designed MES should enhance productivity, lower conversion costs and increase product quality.
Years ago, when I started working in manufacturing, MES was still a relatively new concept for most companies. While many people had heard about MES and the significant benefits, they were lacking the understanding of how to implement it to drive ROI. It’s hard to imagine now, but I can still remember several customer sites where the key shop floor system was Excel or even paper-based records. Many companies had invested in automation and controls, but few were taking advantage of the available electronic data and still relying on operators to manually record information.
In the late 2000s it seemed like everyone was talking about MES. If you were not implementing a new system, you were falling behind your competition. Companies were upgrading or adopting new ERP systems and wanted to connect to the shop floor to leverage that data. They realized that the days of siloing data were in the past. And they were right! MES was going to solve all their problems by providing access to real time data.
Unfortunately, many companies struggled deploying MES solutions. The problem was a lack of understanding on WHAT they wanted to get out of the MES. Many programs failed because there wasn’t a clear vision on what the new solution needed to do and how it was going to benefit everyone who was using it. MES solutions were complex and anything but user friendly. Often the end users (operators and managers) were left in the dark until the system was live in front of them. This first impression was not great for MES and going back to the drawing board was important.
Both clients and vendors need to have a clear picture of what they needed to achieve when implementing an MES and how they would deliver ROI. Essentially, we learned from our mistakes. The next wave of MES projects focused on being more user-friendly. This meant that process for the operator to adopt was smoother and that there was plenty of , time to develop and deploy and which provided measurable ROI. Many solution vendors focused on ease of use and development. Starter kits arrived on the market to help kick start client projects.
The response on the factory floor this time around was much more successful. The difference was a more process- driven approach and model-drivenMES. The idea is to understand the uniqueness of each client, and then leverage the tools to bring them a truly game changing solution. Now plant personnel could focus on making great products rather than spending time doing manual data recording. We could point users to the biggest problem areas in the factory and let them act. Many of these programs did achieve ROI to some degree. Clients were able to increase yield, reduce scrap, and increase the quality of their product. The amount of data collected was astounding and it was all at their fingertips! But we couldn’t possibly predict what would happen next when clients became overwhelmed with data.
– Written by Dan Purcell
Our expert team is here to help you implement the best solutions tailored to your unique needs. Find out more about our MES solutions.